What is a Digital Twin?
Digital Twin, as the name implies, is a digital or virtual model of any physical device or system, which spans the latter’s lifecycle, which it consequently does through real-time data which is fed continuously.
In accordance with the data that is fed into the digital twin, it aids in efficient decision making by employing machine learning, simulation, and reasoning.
For example, a physical object like a reactor in a chemical manufacturing plant is fitted with sensors at the vital areas of functionality like temperature, pressure, volume of reactants etc. These sensors then feed the data onto a digital twin which then runs simulations to get to know the time of completion of reaction, mass of the products and sludge.
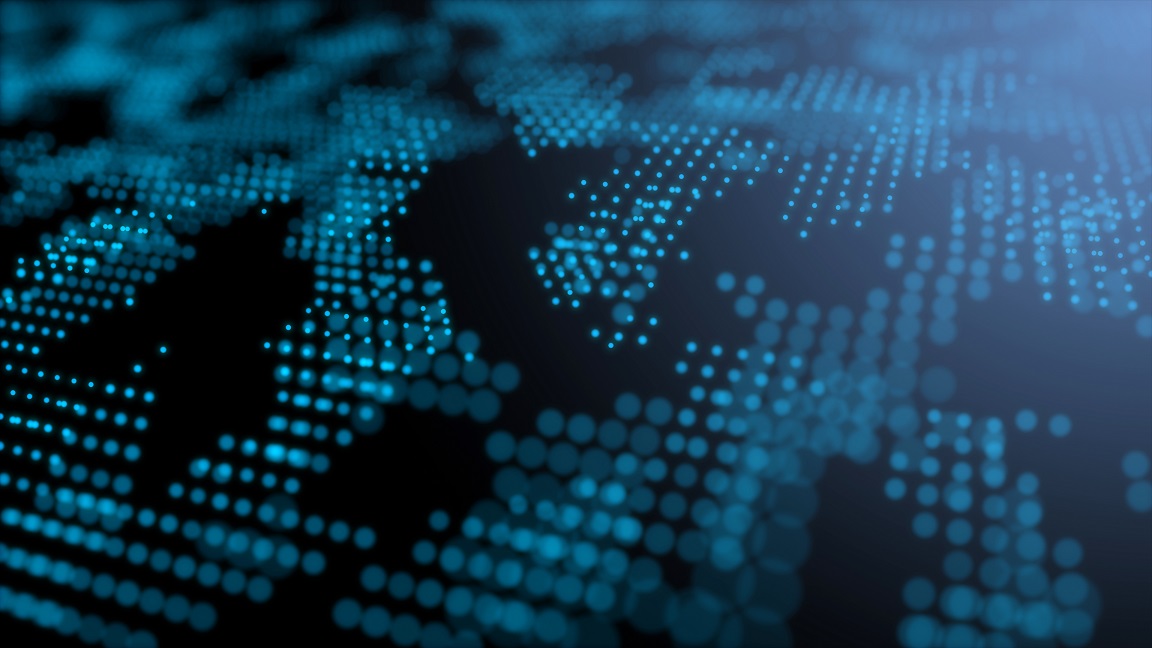
Advent of the digital twin
At a symposium for the Society of Manufacturing Engineers in Troy, Michigan, in 2002, Dr. Michael Grieves made the concept and model of the digital twin public for the first time.
In a 2010 Roadmap Report, NASA's John Vickers referred to the idea of a "digital twin," which has previously gone by other titles (such as "virtual twin").
The physical system or product and the digital system or product are two separate system or product pieces that are connected in the digital twin idea. Information flows and physical sensor flows between the physical system and the digital system, as well as their surrounding physical environment, are some of the links between the two systems.
Digital Twins in Product Development
Digital twin prototype (DTP), digital twin instance (DTI), and digital twin aggregate (DTA) are three of the most prevalent subtypes of digital twins.
- The designs, analyses, and processes used to create a physical product are included in the DTP. A physical product cannot exist without DTP.
- Once a product is built, the DTI serves as the digital twin of each unique instance.
- The DTA is a collection of DTIs that may be queried for statistics and information related to the physical product, prognostics, and education. Use cases dictate the precise data that goes into the digital twins. As a logical construct, the digital twin may contain actual data and information in other applications.
Applications of Digital Twins in various domains
- Power Generation
The usage of digital twins is extremely advantageous for large engines, such as jet engines, locomotive engines, and power-generation turbines, especially when determining whether routine maintenance is required.
- Construction systems
Digital twins can improve massive physical structures, especially during the design phase, such as tall buildings or offshore drilling platforms. Additionally helpful for creating the HVAC systems that run within those structures.
- Manufacturing
It is not unexpected that digital twins have proliferated in all phases of manufacturing, leading items from design to final product, and all steps in between, given that they are intended to mirror a product's full lifecycle.
- Automotive Industry
The automotive industry is also utilizing digital twins. To simulate a connected vehicle before actual production begins, automakers use this technology. This procedure aims to mimic and examine any potential future issues that could arise with the actual car being driven on the road.
- Healthcare
Digital twins are used by the healthcare sector in several contexts, including bed occupancy, patient health data monitoring, and medical equipment usage. It is an innovative technique to help healthcare providers monitor the operational effectiveness of the organization to construct a digital twin of the hospital, its functional infrastructure, and patient care.
Additionally, the genomic code, lifestyle and physiological traits could all be copied and imitated using digital twins. In this manner, patient care can be tailored and personalized based on each patient's unique characteristics.
How can businesses benefit from incorporating Digital Twins?
Digital Twins have been integrated into every realm of business processes and organizations are investing hugely in this regard. And why shouldn’t they?
Digital Twins enable endless simulations so that the stakeholders can test each scenario before attempting the same in real life. In other words, digital twins can be used to prototype products before they are manufactured, lowering product faults, and speeding up the time to market.
It should be possible from an organizational standpoint to examine and evaluate various internal processes from a variety of angles. In this perspective, it is possible to picture a digital twin as encompassing many of the value streams of the company, from production to maintenance and operation to marketing and sales.
The fact that the data provided can be used by numerous constituencies both inside and outside the organization is one of the main advantages in this case.
Digital twins can readily have many access points because they are made entirely of data, allowing each stakeholder to simply access the parts they require. This enables a business, for instance, to grant the specialized access necessary for its operations team, auditing team, and sales team to learn more about the procedures that are important to their respective roles.
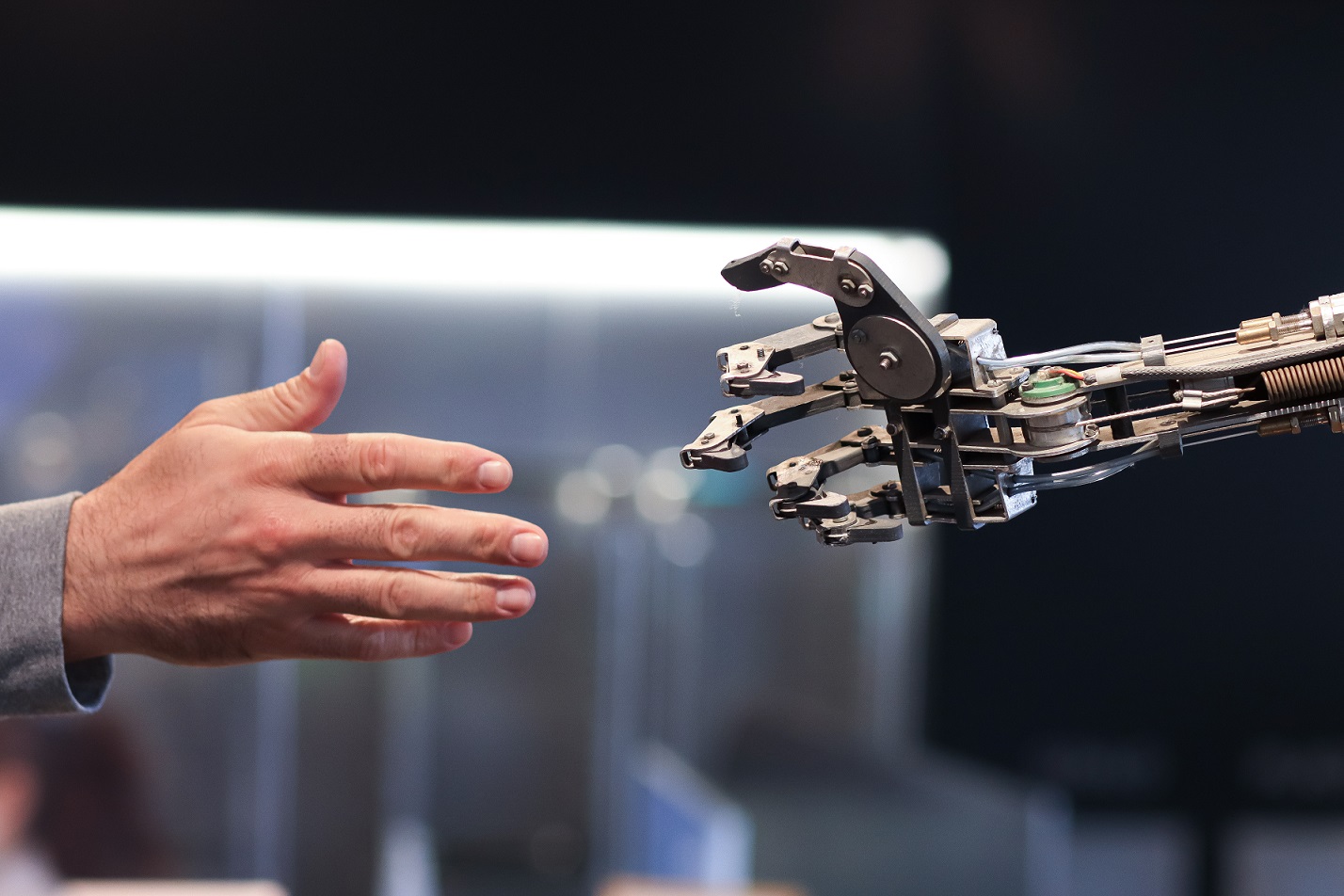
Technology trends shaping the future of Digital Twins
The use of the digital twin as an "operating model" will increase, and soon it is anticipated that it will play an important and widespread role in production.
This human-intelligent system integration is poised to further develop in this decade itself. Organizations have realized that integration of artificial intelligence into business processes is vital when they consider their long-term vision. Digital Twin as an amalgamation of data integration vs business intelligence is what will shape the near future.
Certain start-ups like Tooliqa known for using machine learning and information architecture have leveraged Digital Twins to provide customized solutions to various business use cases, especially for enterprise architecture technology companies, which would help better their processes and reimagine their long-term goals using deep tech and computer vision.
- Virtual Validation: Engineers and designers utilize the technique of virtual validation to put a replica of a product "under test" to satisfy legal requirements, ensure quality, or ensure functional safety. As automakers aim to test new digital technologies in electric and driverless vehicles, the usage of virtual validation is expanding in the automobile sector.
- Generative Design: The design goals, as well as characteristics like performance or spatial requirements, materials, manufacturing processes, and cost limitations, are entered by designers or engineers into generative design tools. The program swiftly generates design alternatives by investigating every variation of a potential solution. With each iteration, it tests innovative ideas and determines what works and what does not.
- AI DevOps: The development of AIDevOps tools enables engineers to deploy models across many targets and guarantee that simulations and predictions are using the most recent model iterations.
Tooliqa specializes in AI, Computer Vision and Deep Technology to help businesses simplify and automate their processes with our strong team of experts across various domains.
Want to know more on how AI can result in business process improvement? Let our experts guide you.
Reach out to us at business@tooli.qa.